Diamond is the strongest natural material. This makes it the most durable material that exists. This property alone is what makes diamond (including synthetic diamonds such as polycrystalline diamond) the ideal material for cutting.
Diamond tools made of polycrystalline are famous for having a longer life-span of cutting and the capability to work at greater cutting speeds and exceptional performance processing non-ferrous materials like aluminium and composites.
Non-ferrous metals that are difficult to machine with standard tools can lead to issues such as wear and tear on tools or low processing efficiency. However, cnc cutting tools, on the other hand, can provide excellent processing performance.
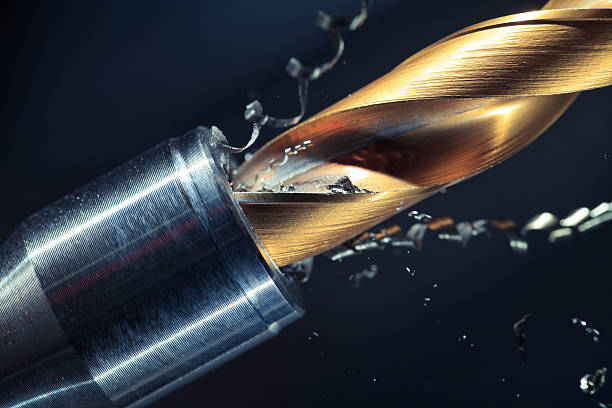
What is Polycrystalline Diamond?
The polycrystalline diamond (PCD) that is not precisely directed, is extremely strong. It is composed of diamond crystals bonded to a substratum containing carbonate tungsten. Synthetic diamonds are produced in a laboratory using a high-temperature and high-pressure sintering process. Cobalt alloys are used to fill the gaps between the grains. The result is extremely stable and retains its shape because of the bonding of individual diamond grains.
The advantages of PCD Tooling
The primary advantages of cutting PCD tools include:
Solid carbide tools have a longer life of the tool and more consistent results. They last from several days or weeks, depending on production levels. But, pcd reamer combination, on the other hand, is designed to last over months which implies that there will be less downtime. This is what makes PCD tools a fantastic option for production facilities with high yields and smaller shops, since the return on investment is quick because of more efficient workflows, fewer tools to change and reduced cycles.
High Speed Performance: Solid carbide tools aren't able to perform at peak efficiency and efficiency up to 10 times more quickly than PCD tools. This allows jobs to be completed more quickly and reduce time to complete the work.
More stringent tolerances: Other finishing processes such as grinding and deburring can be time-consuming and severely impact your bottom line. This could lead to an enormous loss of time, money , and energy. The PCD tooling could be more precise and can hold their cutting edge/form longer than high-speed steel (HSS), which lets you finish more parts in a shorter time and enhance the quality and accuracy.
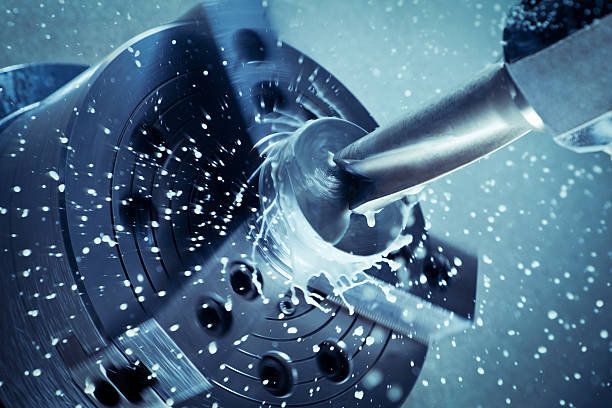
Material Versatility In the past, PCD tools were considered an exclusive product due to the fact they could only be used for a small selection of materials. But advances in manufacturing processes and materials have allowed pcd forming tools to be used in a wide range of applications, including aluminium composites, and abrasive materials.
Surface Finish PCD tools can deliver a high-quality surface finish without needing a second process. The manufacturers can therefore save time and money, while maintaining the same high quality standards.